Подшипники являются надёжными механическими компонентами, которые имеют продолжительный срок службы при условии их надлежащего монтажа и обслуживания. Как следует из открытых данных статистики производителей подшипников, допущенные при монтаже ошибки являются непосредственной причиной досрочного выхода из строя примерно 14% подшипников. Для правильного монтажа требуется опыт, внимательность, чистота рабочего места, использование правильных методов и соответствующих инструментов.
Перед началом монтажа следует спланировать работы, изучить чертежи подшипниковых узлов машины и инструкции производителя оборудования, чтобы:
- определить правильный порядок сборки всех компонентов, образующих подшипниковый узел;
- проверить соответствие типа, размера и исполнения подготовленного к монтажу подшипника требованиям документации на узел;
- подготовить соответствующий смазочный материал в должном количестве;
- назначить соответствующий метод монтажа;
- убедиться в наличие и исправности подходящих инструментов и оснастки.
Работы по монтажу подшипников должны выполняться квалифицированным персоналом. Обязательно наличие и точное соблюдение инструкций по монтажу, которые обычно предоставляются производителем оборудования. При отсутствии можно воспользоваться рекомендациями производителей подшипников или общемашиностроительных справочников.
Чистота рабочего места крайне важна для продолжительного срока службы подшипника. Чистота начинается на складе. Подшипники следует хранить в отапливаемом помещении, защищённом от образования конденсата, потоков воздуха и резких перепадов температур, при относительной влажности воздуха не более 75% и окружающей температуры не более +40°. Подшипники должны храниться без воздействия прямых солнечных лучей, в горизонтальном положении, в условиях полного отсутствия вибрации. Запрещается открывать или нарушать оригинальную упаковку подшипников до начала монтажа. Однако даже при соблюдении всех условий, срок хранения не должен превышать 3-х лет. После истечения срока хранения подшипники подлежат ревизии и, по её итогам, повторной консервации либо утилизации.
По возможности монтаж подшипников следует выполнять в сухом чистом помещении вдали от работающего оборудования во избежание попадания в узел пыли, влаги и металлических опилок. Не вскрывайте упаковку вплоть до момента начала монтажа. Обеспечьте чистоту подшипников и всех сопряжённых деталей, включая смазочный материал и инструменты.
Если монтаж подшипника производится в незащищённом месте, как это часто бывает при работе с крупногабаритными подшипниками, необходимо принять специальные меры по защите подшипникового узла от попадания загрязнений в продолжении всего процесса монтажа. Это можно сделать, накрыв или обернув подшипник и прочие детали промасленной бумагой, плёнкой или фольгой. По окончании монтажа следует немедленно загерметизировать узел, установив штатные уплотнительные устройства и крышки.
Оригинальная упаковка подшипников предусматривает наличие защитного покрытия на поверхности подшипника - консерванта, предохраняющего металлические части от воздействия влаги. В случае, когда консервант химически совместим со смазочным веществом, которым планируется смазывать подшипник при работе, не требуется полностью удалять защитное покрытие на новых подшипниках, и достаточно вытереть посадочные поверхности наружного и внутреннего колец безворсовой тканью. Новые подшипники перед монтажом следует промыть сольвентом и просушить, если консервант не совместим со смазочным веществом. Химическую совместимость консерванта и смазочного вещества можно проверить на основании данных, предоставляемых производителями подшипников и смазочных веществ.
Удовлетворительная работа подшипника будет обеспечена лишь в том случае, если все сопряжённые детали выполнены с соответствующими допусками и не имеют повреждений, поэтому перед монтажом необходимо проверить точность размеров и формы посадочных поверхностей вала и корпуса. Необходимая точность, предъявляемая к сопряжённым деталям, обычно указана в документации производителя оборудования и в каталогах производителей подшипников. Невыполнение требований точности размеров приводит к образованию нерасчётной – слишком сильной или наоборот прослабленной - посадки в соединении подшипника с валом или корпусом, и, как следствие, работе подшипника с недостаточным внутренним зазором или избыточным натягом, либо к провороту подшипника на шейке вала или в корпусе с развитием абразивного износа и фреттинг-коррозии. Запредельное отклонение формы сопряжённых деталей снижает надёжность посадки вследствие уменьшения площади пятна контакта в соединении, а также приводит к искажению внутренней геометрии подшипника, что проявляется падением кинематической точности узла. Порядок проверки фактических размеров и точности сопряжённых деталей будет подробно рассмотрен в следующей статье «Подготовка к монтажу подшипников качения».
Общее требование к процессу монтажа состоит в минимизации прилагаемых к подшипнику усилий во избежание риска повреждения его компонентов. Усилие монтажа ни в коем случае не должно передаваться через тела качения! Немаловажным фактором, как с экономической, так и технической точек зрения, является высокая скорость проведения монтажных работ. Абсолютный приоритет отдаётся безопасности для проводящего монтаж персонала. Чтобы свести к минимуму опасность несчастного случая при монтаже, рекомендуется следовать инструкциям производителя оборудования и изложенным ниже рекомендациям.
Для перемещения подшипников, особенно нагретых или замасленных, необходимо использовать защитные тепло- или маслостойкие перчатки. Также может представлять опасность горячий смазочный материал в случае его утечки из уплотнённых подшипников.
С нагретыми, а также с крупногабаритными подшипниками сложно и небезопасно обращаться в одиночку или даже вдвоём. В этом случае для подъёма и перемещения подшипников нужно использовать грузоподъёмное или транспортировочное оборудование (рис. 1,2,3), предназначенное для обращения с подшипниками.
![]() |
![]() |
![]() |
Крупногабаритные подшипники следует охватывать мягкой стропой по наружному диаметру с её фиксацией «на удавку» (рис.4), недопустимо захватывать такой подшипник за одну точку (рис.5), поскольку это может необратимо деформировать кольца. Резьбовые отверстия в кольце крупногабаритных подшипников могут быть использованы для установки рым-болтов, нагрузка от стропы должна быть приложена вдоль оси рым-болта (рис.6).
![]() |
![]() |
![]() |
Пружина между крюком и лебёдкой поможет выровнять подшипник и смонтировать его без перекоса (рис.1).
При монтаже крупногабаритного массивного корпуса на подшипник, который уже смонтирован на валу, рекомендуется использовать трёхточечную подвеску для корпуса с возможностью регулировки длины одной стропы. Это облегчит выверку отверстия корпуса относительно наружного кольца подшипника.
В зависимости от назначения машины и конструкции узла, сопряжение подшипника с валом и корпусом может быть предусмотрено по посадке с зазором, посадке с натягом или по переходной посадке. В соединении внутреннего кольца подшипника с валом чаще всего применяется тугая посадка - с гарантированным натягом, при этом способ реализации тугой посадки определяется формой отверстия подшипника. В случае отверстия цилиндрической формы, посадка с натягом образуется сочетанием фактических размеров посадочной шейки вала и отверстия подшипника, что регулируется полями допусков, назначаемых для вала конструктором машины соответственно её функционалу, а для подшипника - изготовителями подшипников согласно международным стандартам. В случае конусного отверстия, натяг в посадке на вал может быть отрегулирован в достаточно широких пределах при монтаже путём относительного смещения внутреннего кольца подшипника и сопряжённой детали – вала или втулки. Контроль величины натяга осуществляется косвенным образом: измерением осевого смещения кольца, определением изменения внутреннего радиального зазора в подшипнике, наблюдением за показаниями установленных на внутреннем кольце подшипника тензодатчиков и некоторыми другими. Различие в способах получения тугой посадки в зависимости от формы отверстия внутреннего кольца подшипника обуславливает существование разных методов монтажа.
Принципиально имеется два основных способа монтажа подшипников качения.
Первый, называемый «холодным механическим монтажом», состоит продвижении подшипника вдоль сопряжённой детали подшипникового узла - вала, втулки или корпуса - путём приложения монтажного усилия к тому кольцу подшипника, которое монтируется по посадке с натягом. Усилие к торцу кольца прикладывается в осевом направлении, величина усилия должна быть достаточна для преодоления силы трения в посадке. Источником усилия может быть монтажный молоток (рис.6), монтажная гайка с ключом (рис. 8, 9), винтовой (рис. 10) или гидравлический (рис.11) пресс.
![]() |
![]() |
![]() |
![]() |
![]() |
![]() |
Обязательным является применение оснастки, обычно в виде специальных втулок, обеспечивающей передачу монтажного усилия безопасно для подшипника и монтажника (рис. 12).
![]() |
![]() |
Способ применяется для монтажа мелких и средних подшипников с цилиндрическим или конусным (рис. 8) отверстием. Основным недостатком этого способа является абразивный и адгезивный износ сопряжённых поверхностей, что ведёт к изменению их диаметров и отклонению фактической посадки от расчётной, особенно когда вал или корпус используются неоднократно.
Разновидностью данного способа является монтаж с применением гидравлической гайки, конструктивно представляющей собой специализированный гидравлический пресс. При монтаже тело гидрогайки навинчивается на резьбовой участок вала (рис.12) или закрепительной втулки (рис.14, 15), а кольцевой плунжер упирается в торец внутреннего кольца подшипника или стяжной втулки (рис.16). Также возможен вариант, когда гидрогайка навинчивается на резьбу стяжной втулки, а плунжер упирается в монтажную шайбу (рис.13). При подаче масла в полость гидрогайки плунжер выдвигается и сообщает движение подшипнику. Усилие монтажа пропорционально площади плунжера и давлению, развиваемому насосом, и может быть точно отрегулировано в широких пределах. По окончании монтажа гидравлическая гайка заменяется на обычную фиксирующую. Способ применяется для монтажа средних и крупногабаритных подшипников с коническим отверстием, установленных как непосредственно на коническую шейку вала, так и на закрепительные или стяжные втулки.
![]() |
![]() |
![]() |
Для снижения силы трения в посадке во время монтажа крупногабаритных подшипников применяется инжекция масла, т.н. гидрораспор, создающий тонкую разделительную плёнку монтажного масла между сопрягаемыми поверхностями (рис.17). Масло в зону контакта подаётся специализированным насосом высокого давления – инжектором - через систему каналов и канавок, предусмотренных конструкцией вала (рис.17,18), корпуса или втулки (рис.13, 19, 20). По завершении монтажа и отсоединении инжектора масло в течение нескольких минут полностью уходит из сопряжения, вследствие чего образуется плотная посадка и соединение металлических деталей непосредственно друг с другом.
![]() Рис.17 |
![]() |
Применение гидрораспора при монтаже позволяет на порядок снизить требуемое осевое усилие монтажа, что упрощает и ускоряет проведение монтажных работ. Ещё более широко гидрораспор применяется при демонтаже подшипников.
Вторым принципиально отличным способом является монтаж с нагревом. Он основан на физическом явлении увеличения геометрических размеров тел, в частности, металлических деталей, при увеличении их температуры. Например, нагрев внутреннего кольца подшипника увеличивает диаметр отверстия настолько, что посадка на вал с натягом на время монтажа превращается в посадку с зазором, и это позволяет без усилий смонтировать подшипник на вал. При последующем остывании кольца его диаметр уменьшается, кольцо обжимает вал, и образуется предусмотренная конструкцией узла посадка с натягом. Требуемая разница температур между кольцом подшипника и валом или корпусом зависит от величины натяга и диаметра посадочного места. В большинстве случаев для монтажа достаточно иметь разницу температур сопрягаемых деталей около 80° - 90°С.
Для нагрева подшипников применяются различные устройства, общим требованием к которым является точный контроль температуры, поскольку чрезмерный нагрев необратимо ухудшает внутреннюю структуру подшипниковой стали, что снижает её твёрдость и радикально сокращает ресурс подшипника. Поэтому категорически запрещается нагревать подшипники открытым пламенем газовых горелок, паяльных ламп и аналогичных устройств с неконтролируемой температурой (рис.21). Также не рекомендуется применять для нагрева подшипников строительный фен. Не следует нагревать подшипники с уплотнениями выше 80°С и открытые – выше 120°С.
![]() |
![]() |
Для нагрева небольших подшипников или корпусов можно использовать электроплиту с диапазоном регулировки температуры 50°С -200°С (рис.21). Чтобы обеспечить равномерный нагрев, подшипники нужно несколько раз переворачивать.
Нагревательные шкафы (рис. 22) обычно используются для одновременного нагрева большого количества малогабаритных подшипников или нескольких подшипников различного размера, а также малогабаритных корпусов. Шкафы должны быть оборудованы термостатом и вентилятором, перемешивающим воздух внутри шкафа для равномерного распределения температуры.
Инфракрасные радиаторы (рис.23) представляют собой чистый, безопасный и эффективный способ нагрева малогабаритных тонкостенных корпусов Инфракрасный радиатор располагается в отверстии корпуса, и требуется непродолжительное время для достаточного нагрева корпуса, поскольку посадка наружного кольца подшипника в отверстие корпуса редко бывает с большим натягом. По достижении необходимой температуры радиатор выключается и быстро извлекается из корпуса, а в отверстие вставляется холодный подшипник.
![]() |
![]() |
Гибкие нагревательные панели (рис. 24) являются отличным и безопасным решением для нагрева корпусов без применения сложных установок. Они выполнены из эластичных материалов в виде гибких ковриков различных форм и размеров. Нагревательными панелями можно накрыть корпус сверху, поместить их внутри корпуса, или использовать в качестве плоского нагревателя снизу.
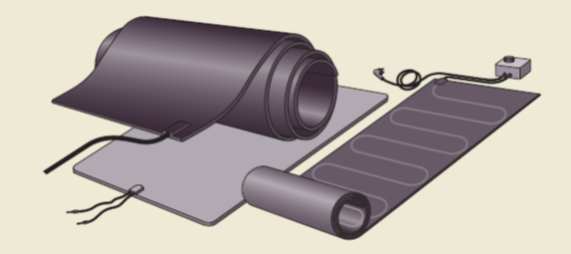
Рис. 24
Алюминиевые нагревательные кольца, (рис. 25), изначально предназначенные для демонтажа внутренних колец цилиндрических роликоподшипников типов NU, NJ, NUP, также могут использоваться для монтажа перечисленных подшипников.
![]() |
![]() |
Нагрев в масляной ванне ранее широко применялся для подшипников всех размеров и малогабаритных корпусов. Сейчас этот метод более не рекомендуется по причине низкой экономичности, небезопасности и отрицательного влияния на окружающую среду. Кроме того, нагрев в масляной ванне неприменим для подшипников со встроенными уплотнениями по причине возможного смешения заложенной в подшипник смазки с маслом из ванны.
Наиболее современным, эффективным и универсальным является метод индукционного нагрева. Принципиально индукционный нагреватель (рис. 26) представляет собой трансформатор, первичная катушка которого через управляющее устройство подключена к источнику электроэнергии, а кольцо подшипника является короткозамкнутым витком вторичной катушки. Система управления контролирует температуру кольца с помощью установленного на нём термометра, что позволяет обеспечить быстрый и точный нагрев. Обязательной функцией является принудительное автоматическое размагничивание подшипника по окончании нагрева для уменьшения вероятности попадания в него стальной пыли и стружки. Индукционные нагреватели применяются для подшипников, а также корпусов, втулок, полумуфт, зубчатых колёс и других металлических деталей с замкнутым контуром.
В случае применения метода монтажа с нагревом особое внимание следует уделять технике безопасности. Использование специальных теплозащитных перчаток является обязательным.
По окончании монтажа следует произвести первоначальное смазывание подшипников, установить уплотнительные устройства, предусмотренные конструкцией узла, и закрыть узел штатными крышками. Перечисленные операции должны быть проведены по возможности быстро, чтобы сохранить чистоту во внутреннем пространстве подшипникового узла.
В некоторых случаях дополнительно требуется настройка внутреннего натяга или зазора в узле, а также балансировка ротора и выверка соосности по отношению к приводу либо к исполнительному механизму.
Важным аспектом эффективного технического обслуживания является документирование всех процессов, и это в полной мере относится к операциям монтажа подшипников качения. Настоятельно рекомендуется вести протокол проведения монтажных работ или журнал ремонта, в который внести следующую информацию:
- точное однозначно идентифицируемое название, положение и состояние оборудования, машины, узла, опоры, месторасположение монтируемого подшипника;
- полное обозначение подшипника, его соответствие требованиям конструкторской документации или инструкции по ремонту и/или техобслуживанию оборудования, на котором производится монтаж;
- результаты измерения размеров и формы шейки вала, отверстия корпуса и других сопряжённых с подшипником деталей узла с общим выводом касательно соответствия фактических размеров требованиям конструкторской документации или инструкции по ремонту и/или техобслуживанию оборудования;
- описание состояния подшипника и, при наличии, закрепительной/стяжной втулки с записью полного обозначения, наблюдений касательно отсутствия механических повреждений, коррозии, наличия консерванта, возможности свободного вращения, и, если проводились измерения, то с указанием величины внутреннего радиального или осевого зазора;
- название и краткое описание выбранного метода монтажа с полным перечнем использованного оборудования, инструментов и оснастки, с записью всех параметров, сопровождающих монтаж, таких как температуры нагрева и окружающей среды, осевое смещение или угол поворота гайки, давление в гидрогайке, изменение внутреннего радиального зазора и т.д.
- параметры первоначального смазывания, а именно полное обозначение смазочного вещества, название производителя, состояние вещества и его соответствие нормам, количество, заложенное в подшипник и в узел, перечень применённых инструментов и методов смазывания;
- параметры настройки узла – величина внутреннего натяга или зазора, точность балансировки и центровки, соответствие фактических параметров требованиям инструкции производителя оборудования, перечень применённых инструментов и методов;
- подробный перечень всех отклонений от требований инструкции по монтажу, которые фактически были допущены, с описанием причин и обоснований допустимости этих отклонений;
- перечень всех участников монтажа с указанием ФИО, должности и квалификации;
- дату, место, время начала и окончания монтажа;
- перечень нештатных событий, сопровождавших монтаж или оказавших влияние на проведение монтажа, в частности, проведение работ на соседнем оборудовании, аварии, авралы, отключение электроэнергии, природные и погодные аномалии и т.д.
Фото и видеофиксация является полезным дополнением к протоколу проведения монтажных работ. В дальнейшем содержащаяся в протоколе информация может быть использована для повышения эффективности технического обслуживания и работы предприятия в целом.